Many industrial professionals think braided packing is an inferior and outdated fluid sealing technology. But braided packing a good choice for many applications. With proper product selection, reliable performance can typically be assured. However, a thorough equipment inspection before installation is critical. The components described in this article should be reviewed and documented on every work order and corrected before any repacking of the pump to achieve maximum performance.
The shaft or sleeve is one component that everyone checks for wear, but they may not understand how to inspect it correctly. For an effective inspection, first examine the shaft and see where the predominant wear has occurred. Is it in front of the lantern ring or on the gland side?
Front-side wear in slurries is most likely caused by a loss of flush water, often because the lantern rings or flush water lines are plugged. The wear could occur if personnel who add the packing rings do not completely repack the stuffing box.
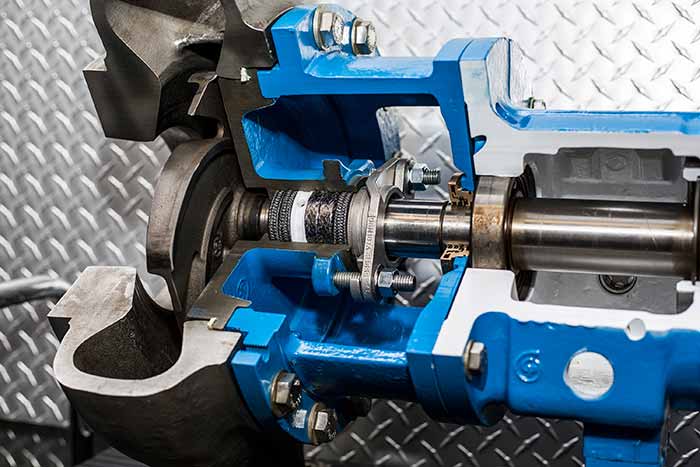
If the shaft or sleeve wear is on the gland side, the packing rings may not have been properly seated, causing the outside rings to burn and glaze. Alternatively, over tightening the packing may have cut off all flush water lubrication. When should end users add or replace a sleeve? Some wear is normal, but if it exceeds 1/32 inch, the user may consider adding or replacing the sleeve during the next service.
The size and condition of the stuffing box is rarely checked. It can be a real problem especially in rebuilt, large-capital equipment. Checking the sizing on critical equipment with telescoping gauges is important to ensure the correct cross-section packing is installed.
On smaller equipment, the installer needs to pay close attention to the resistance of the packing while inserting it into the stuffing box. There should be resistance, and it should take some effort to install. The packing must never just “fall” into the stuffing box. If it does, the installer should make sure the correct cross section is being used.
The condition of some equipment is almost never checked. These components include the gland follower, lantern rings and stuffing box throat and/or throat bushings.
To have a full understanding of the critical nature of these components, end users must understand the principles and the function of braided packing. Packing has a dynamic surface along the inside diameter at the sleeve surface and a static surface on the outside diameter along the stuffing box bore. The inside surface along the sleeve is designed to control flush water leakage at a controlled rate of 10 to 12 drops per minute per inch of shaft size. The outside surface at the stuffing box bore is static and, for all practical purposes, is a gasket. No fluid should ever leak from this area.
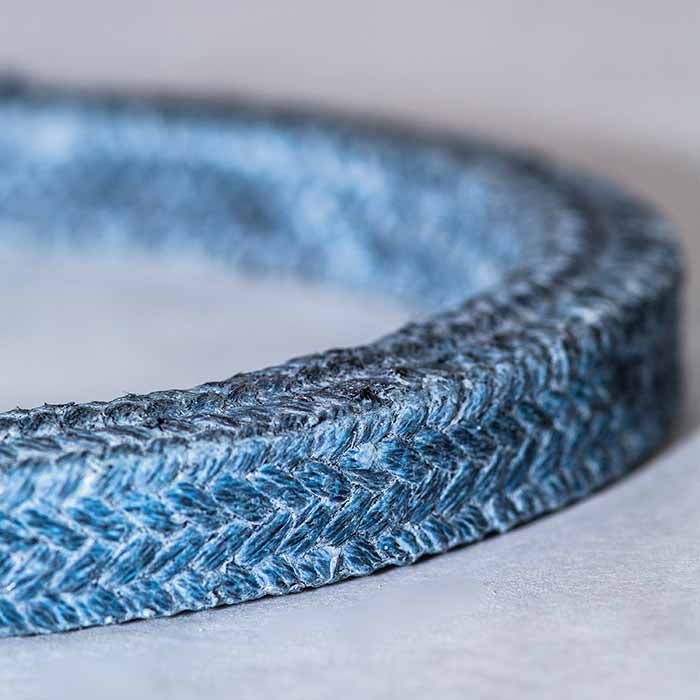
In principle, the packing is compressed by the nose of the gland follower against the throat of the stuffing box bushing or bottom causing it to expand radially against the sleeve and stuffing box bore. Because of these dynamics along the shaft, the condition of the gland follower, lantern ring and stuffing box throat are important. The main issues with these components are wear and clearance loss.
Because they are designed by the original equipment manufacturers (OEM) to have certain fits and clearances, wear causes the loss of these specified fits resulting in improper loading of the packing. The loss of load transfer from the gland follower through the lantern ring against the bottom of the stuffing box or throat will result in excessive leakage and premature packing failure.
The condition of the internal pump components is directly related to the performance and reliability of any fluid sealing program. If end users adhere to the best practices outlined in this article, excessive leakage caused by improper packing installations will be all but eliminated resulting in less equipment downtime because of gland water issues.