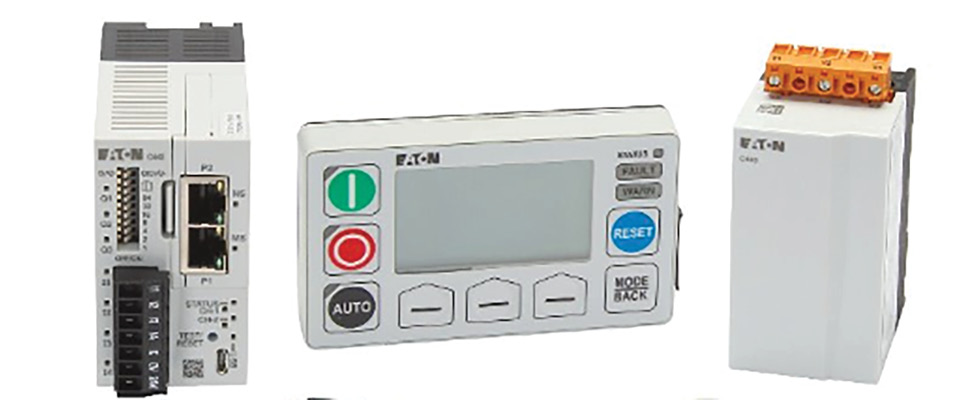
The efficient operation of pumps is crucial in factories and heavy machinery. Pumps play a fundamental role in various applications, from water treatment plants to manufacturing facilities. However, the reliability of these pumps can be compromised when subjected to dead head or underloaded conditions.
Why Protect Pumps From Low Power (Dead Head)?
Dead head occurs when a centrifugal pump operates without any flow through it, typically due to a closed discharge valve or a blockage in the line. In such situations, the pump ends up recirculating the same water, causing a gradual rise in water temperature. Prolonged operation under dead head conditions can lead to excessive heating, resulting in damage to expensive seals and a significant reduction in the pump’s life span.
Why Is Dead Head Hard to Detect?
Detecting dead head conditions is challenging, as conventional methods like float switches fail to recognize the issue since water levels do not decrease. The key to accurate pump protection against dead head damage is that the motor load decreases. Two methods are available to determine motor load: motor current and input power. However, monitoring current for underloaded conditions is not effective because current is nearly constant up to 50% of the motor load. Current is high even at light loading, and the power factor is high as current is flowing to the motor but is not doing useful work (power).
Best Practices for Protecting Pumps
To safeguard pumps from the damaging effects of dead head and other underloaded conditions, it is crucial to adopt the best practices in pump protection. Traditional methods, such as float switches, are ineffective for dead head detection. Instead, the focus should be on monitoring motor load, with an emphasis on detecting decreases in power.
Motor management relays offer a comprehensive solution by providing current, voltage and power-based monitoring and protection. Unlike traditional methods that rely on current monitoring, which is less effective at detecting light loads, a motor management relay leverages power-based detection. Power varies linearly across the motor load range, making it an extremely reliable method for promptly identifying even small decreases in motor load.
Predictive Features on the Horizon
The industry is witnessing the emergence of predictive features that enhance pump protection. Motor management relays offer predictive features to detect and prevent dead head conditions. By continuously monitoring power, the relay can predict potential issues and take proactive measures to safeguard the pump. Some relays are able to detect pump cavitation and motor-related issues through the use of motor current signature analysis.
Some motor management relays allow users to set the trip point to a desired percentage of rated power. This level of customization ensures the relay is tailored to the specific requirements of the pump system. Moreover, the relay provides separate warning and trip levels with customizable delays, adding an extra layer of flexibility to the protection mechanism.
A Comprehensive Pump Protection Solution
Some motor management relays go beyond dead head protection. They offer a single, compact solution for pump protection while also addressing other critical motor protection aspects. Thermal overload, ground fault and various current- or voltage-based protections are seamlessly integrated into the motor management relay. Protecting pumps from dead head and underloaded conditions is paramount for ensuring the longevity and efficiency of industrial processes.