Specialized software helps end users address problems before they happen.
05/05/2015
At combined-cycle power plants, a problem in even the smallest piece of equipment can cause significant downtime and lost production. Valves, in particular, must operate at peak performance to ensure consistent plant operation. With the help of remote monitoring software solutions and related support, power plant management teams can ensure that all equipment is operating efficiently and address potential problems before they result in costly downtime.
Failing Servo Valve
In the summer of 2013, a remote monitoring software solution detected a small increase in the difference between the command and feedback of a valve on a combustion turbine at a combined-cycle power plant. The difference in feedback increased from approximately 1.6 percent to about 2.9 percent. At the same time, the differential on the other gas valves appeared to be stable and tracking around 0.5 percent (see Figure 1). The software solution company notified the end user of this issue in a weekly report and began tracking this measurement on weekly calls.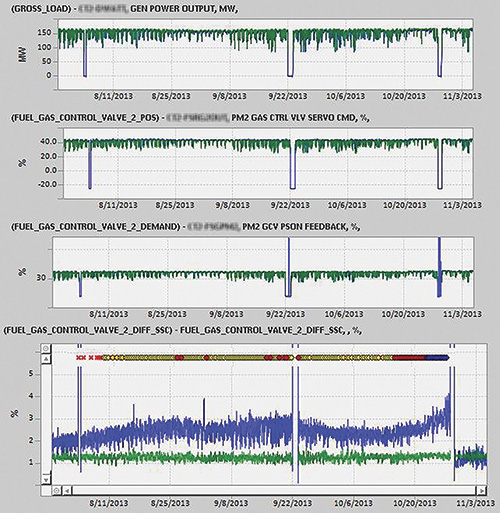
Tripped Purge Valve
In early November, this same software solution detected that the hydrogen gas pressure on a generator was dropping rapidly. Values were expected to operate at approximately 31 pounds per square inch gauge (psig) (3.2 bar). Actual values, however, were measured as low as 28 psig (2.9 bar) (see Figure 2). The software company sent a high-priority notification to the end user and began tracking this issue on weekly calls.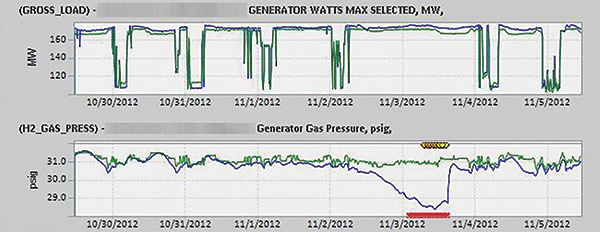