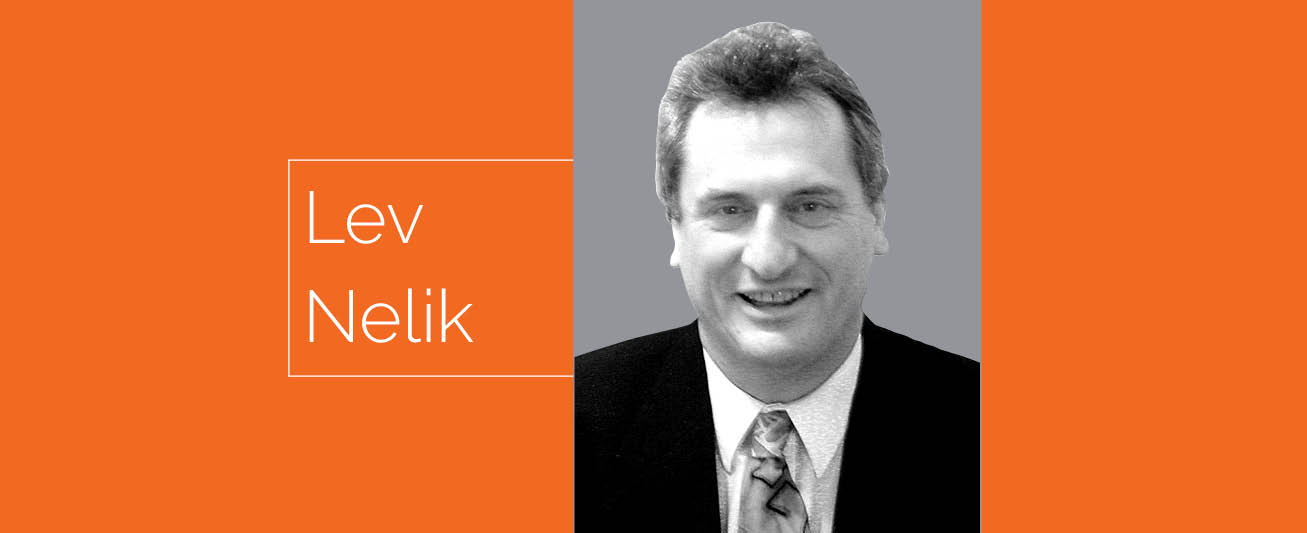
In the March and June issues of Pumps & Systems, we started discussions of repairs and upgrades, and I was asked to include interesting (and informative) examples of how decisions on picking one level versus another are made. In response, I have included an extract from the VPRS Standard, presenting one such interaction that may shed more light on actual live examples of how such decisions are made (or not made), with quantifying analysis with numbers, to substantiate and balance technical aspects of reliability versus the economics of choosing a path forward.
TR:
We have had a series of pumps in our shop from a water treatment plant which all had severe corrosion from the chlorine addition to the water. I have attached a couple of pictures of what the impellers look like. I thought they might make good figures and pictures for the specification.
Interestingly enough, we are using two separate methods to address the damage for the rebuilds. Due to lead time issues, the first pumps utilized the same bronze impellers initially installed except with a nickel coating. The remaining pumps were rebuilt with 316 stainless steel (SS) impellers. Despite the claims from the electrocoating facility, the thickness of the coating applied to the impellers ranged between 0.001 inches and 0.009 inches, so we had to set the clearances with new bowl rings.
Best Regards,
TR
Sales Engineer, RT Company
DR. PUMP:
Thanks for sending pictures. I agree, it would be a good idea to add “damage examples” to the spec body—people often like “to see stuff.”
As a curiosity, how would you compare (at least as a rough estimate) the life of these impellers:
(a) originally (what type of bronze metallurgy?)
(b) coated with nickel coating
(c) 316 SS (was it 316 or 316 L?)
Also, can I copy your email to other committee members? I think folks might be interested as well.
Dr. Lev Nelik, P.E.
Technical Director
International Center for Pumping
Machinery Research and Development
SCE College of Engineering
Beer Sheva, Israel 84746
+972-50-865-0451
pumpingmachinery.com
TR:
I’m afraid it’s very tough to gauge the life of the impellers in this service. We have contradicting accounts from the plant about whether there was a high chlorine concentration for a short time period during the first weeks/months of the plant operation or whether the corrosion damage took place slowly over the course of the 12 years the pumps were in service.
For a high-chlorine environment, we suggested the 316 L impellers as the best option and electroplated nickel as a more cost-effective and, in this case, more timely option. The nickel coating is very thin and, on wear spots, provides a location for the corrosion to begin quickly.
Of course, you’ll notice from the pictures, the thin and high-flow area vanes sustained the most damage. The bronze impellers originally supplied are ASTM B584 Grade C903.
Finally, yes, feel free to share this with the group.
Best Regards,
TR
Sales Engineer, RT Company
DR. PUMP:
Very interesting. Again, thank you for the photos as these will greatly enhance our VPRS spec next edition (rev.1). What you presented is even more interesting than that, and I hope you can enlighten us on this further (perhaps over time). I have always been a big fan, personally, of factual field data—not only book theory. Your examples provide exactly that—real-life examples and facts.
This is why it would be very interesting to compare life (even if it is somewhat approximate, with some simplifying assumptions). From what you tell me, four pumps in six months—this would mean that your first note that perhaps the damage was done at the first few months (12 years ago) is not an issue.
If the damage was done initially (during high chlorine content) but the impellers are coming to the shop only now, that would imply they got damaged quickly and then stayed damaged for 12 years (during which chlorine was okay). So, let’s clarify further:
- How many of these pumps do you have? When were they first installed? (12 years ago?)
- How many pumps came to the shop in 12 years? Have they been coming relatively periodical, or are they starting to come only now (after 12 years in service)?
- When and how many impellers have you coated and installed, and how are these doing?
Same as above for 316 SS
Thank you for your interesting case.
Dr. Lev Nelik, P.E.
Answers below:
1. These four pumps were all installed 12 years ago and have not been out of service until now. We have the last pump in our shop now. The other three have all been here in the last six months.
2. All four pumps came into our shop between the fall of 2021 and spring of 2022. They were all duplicate pumps, and this was first time out of service for all four.
3. The first two pumps were rebuilt with standard bronze impellers (as were installed originally) but with a nickel coating. Once those two pumps were back in service, the remaining two pumps were able to be removed from service to be rebuilt with the 316 SS impellers. The 316 SS impellers had a very long lead time, so we ordered them in fall 2021 for the repair in spring 2022.
4. Covered above.
Feel free to give me a call if you think it would be beneficial.