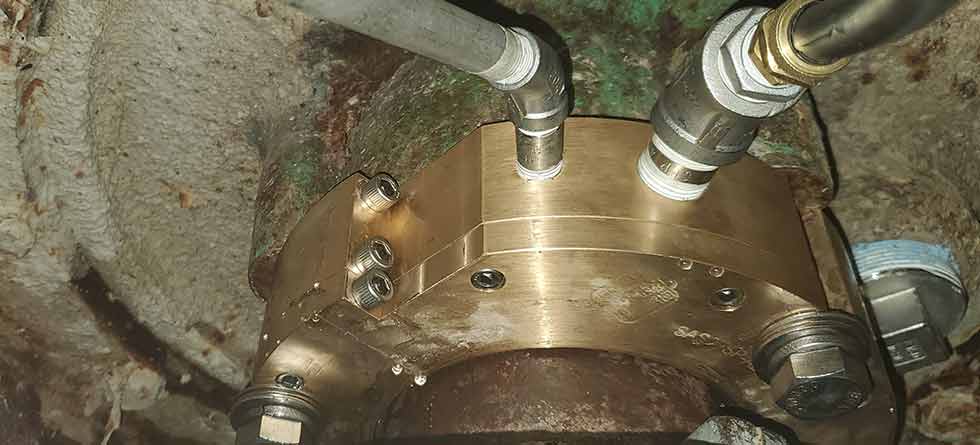
Large bottom- or side-entry mixers and agitators often used in paper and food production tend to be difficult to seal. When the shaft enters through the bottom or side of the equipment, eventual leakage is virtually guaranteed over time. Sealing with packing or mechanical seals presents several challenges:
- The product contacts the sealing element, leading to accelerated wear of the sealing components and the shaft/sleeve of the machine.
- This wear leads to product loss, seal failure and increased operating costs.
- The leaked product introduces safety and sanitation problems, slip/fall risks and housekeeping and cleaning issues.
In food and paper production, shaft movement is another issue. In both process industries, large amounts of ingredients may be dropped into the equipment causing the shaft to move and vibrate. This movement may damage packing and mechanical seals. This leads to downtime to replace the seal, only to restart the cycle of wear, damage, leakage and replacement once the asset is restarted. How can plants end this cycle?
Air Seals
An air seal, which does not contact the shaft or sleeve, is designed to accommodate misalignment that may occur when heavy ingredients and materials are dropped into the bowl. Packing may fret the shaft or sleeve and create leakage paths. Mechanical seals may be damaged by the shaft movement and allow for leaks. Eventually, the product is no longer sealed, and it ends up on the floor. Air seals have been used in dry and wet applications, including hydrapulpers, agitators, mixers and blenders.
How It Works
Air seals use engineered clearances and directional flow paths to create uniform pressure and velocity profiles. These clearances and flow paths generate a pneumatic seal. To accommodate the inherent misalignment that may be present in many food and paper industry applications, a floating throttle is used in the seal that handles 0.0625-inch parallel and 1.5 degrees of angular misalignment. The internal pressure/flow profile is controlled and forms a circumferential boundary layer for air between the throttle and the shaft/sleeve.
This air boundary mitigates any damage that would occur because of shaft movement or misalignment by allowing the throttle to float.
No Maintenance Required
If airflow remains continuous, these air seals require no maintenance. By design, product will not enter the seal or throttle area, so no damage is caused by contamination. Its material of construction keeps wear and corrosion from occurring.
However, system upsets such as power outages and air disruptions do occur. If the air supply is turned off during operation, product may enter the seal. This maylead to the internal air passageway becoming clogged, disrupting the uniformity of the pressure profile. Should this happen, seal disassembly may be required. It can be easily disassembled, cleaned and reassembled.
Air seals improve operations within many industries—two that experience repeat successes are food production and pulp and paper mills.
and bacterial growth at an East Coast animal cracker producer.
Solving Problems With Animal Cracker Dough
An East Coast animal cracker producer experienced significant issues with its dough blender. Dough can be problematic to contain because it oozes through seals, squeezing out water and leaving behind a floury/doughy film. This film accumulates and hardens. Besides lost product and the hardened, difficult-to-clean film, bacteria accumulate and grow in the moist environment.
The leaks were persistent, leading to significant product loss and housekeeping issues. The seal components were regularly replaced, tying up maintenance hours and incurring costs for new seals.
Two years ago, an air seal (Image 2) was installed to replace the rubber OEM seal. Since then, leaks have been eliminated. The seal has operated leak- and maintenance-free with no component replacement or downtime required. Housekeeping issues were mitigated as well. The animal cracker producer has since upgraded two other blenders (one with a contacting air seal) at the facility and seen the same results. With this new seal technology, kids (and kids at heart) are happy because animal crackers continue to flow off the line.
Eliminating Costs & Safety Risks at a Midwest Mill
In pulp and paper mills, pulpers (also called hydrapulpers) are large agitators that mix pulp, recycled paper or cardboard into a slurry of water, pulp and chemicals to create paper. Imagine heavy batches of recycled paper being dropped into the bowl. Shock, vibration and shaft movement are inevitable.
In one Midwest mill, leaking pulp caused the failure of a gearbox, which had to be rebuilt at a cost of $60,000. The pulper also had to be repacked when leakage rates became too high and the packing life was exhausted. This exhaustion happened much quicker because of the harsh nature of the pulper and the shaft movement. Product was consistently lost. While this was an additional cost, the team did not make the effort to define how much was lost during a year.
With the gearbox rebuild, packing purchases and product costs, the plant was losing money. This did not include the losses incurred each time the process was down to replace the packing, which was more frequent than is typical.
In addition to the financial losses and downtime, safety risks and housekeeping problems arose. The leaked pulp on the floor was slick by itself, but slime and mold formed as well—making the area unsafe and slippery to walk on. Therefore, frequent cleanup was required.
The plant team had enough. They decided to install a noncontact air seal on a pilot pulper to see if results improved. To date, the air seal has eliminated pulp leakage. The packing replacement costs and downtime are no longer required. The gearbox no longer has pulp leaking onto it, so its life will be extended.
In addition to these measurable improvements, the process will no longer lose product. While the exact amount of lost pulp was not captured by the team at the mill, this stoppage will decrease costs, waste and housekeeping requirements.
With the development of air sealing technology, end users will experience a reduction in operational costs. These seals have a lower life cycle cost and improve the life of the equipment on which they are installed because they mitigate maintenance; minimize equipment repair and downtime; decrease the cleanup and elimination of leaked product; and provide a safer work environment.
References
1. Third-party CFD analysis by MSC software, mscsoftware.com